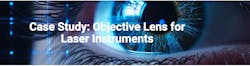
Case Study: Objective Lens for Laser Instruments with Wavelengths (350-850nm) in Medical Devices
Introduction
Avantier, a leading custom optics company, recently undertook a challenging project to design and produce objective lenses for a laser instrument used in a medical device. The client’s specific requirements included an effective focal length (EFL) of 10mm, numerical aperture (NA) of 0.5, a working distance exceeding 22mm, and the ability to handle laser wavelengths ranging from 350 to 850 nm.
Customer’s Challenge
The client approached Avantier with a unique set of challenges. Firstly, the 0.5 NA requirement was driving up costs significantly. Additionally, the materials commonly used for lenses proved ineffective for 350-nanometer laser applications. The use of conventional glass at this wavelength resulted in strong absorption, and opting for i-line glass, while solving the absorption issue, would considerably escalate the overall lens cost.
Avantier’s Approach
Avantier meticulously analyzed the customer’s requirements and challenges to formulate an innovative approach. The project involved multiple lasers, each operating at different wavelengths and field angles. Avantier’s team addressed the 0.5 NA challenge by implementing a novel design that not only met the specifications but also allowed for cost reduction.
Mitigating Material Ineffectiveness
Recognizing the inefficacy of traditional lens materials for 350-nanometer laser applications, Avantier engineers embarked on a comprehensive material selection process. They explored alternative materials that not only minimized absorption but also contributed to cost efficiency. This strategic choice of materials was pivotal in overcoming the absorption challenges, ensuring the lenses performed optimally across the entire specified wavelength range.
Reducing Costs
Avantier’s commitment to cost-effectiveness went beyond material selection. The team implemented a design strategy that allowed for the reduction of multiple optical components without compromising performance. By optimizing the design specifications, Avantier was able to relax axial color tolerances to +/-100um, and even +/-200um, thereby reducing the overall length of the lens. This not only streamlined the manufacturing process but also contributed significantly to cost reduction without compromising the quality of the final product.
Performance Optimization
A critical aspect of the project involved optimizing the lens design for multiple laser wavelengths. Avantier engineers utilized Modulation Transfer Function (MTF) diagrams for laser wavelengths at 350 nm (Figure 1 and 2) and 850 nm (Figure 3 and 4). The laser beams were focused theocentrically on the image plane, ensuring precise separation of laser spots in the vertical direction with approximately 100 um spacing. This meticulous optimization contributed to the overall success of the project, meeting and exceeding the client’s expectations.
Conclusion
In conclusion, Avantier’s innovative approach to the design and production of objective lenses for laser instruments used in medical devices, spanning wavelengths from 350 to 850 nm, exemplifies the company’s commitment to excellence and cost-effectiveness. By addressing the challenges posed by the 0.5 NA requirement and the ineffectiveness of traditional lens materials for certain laser wavelengths, Avantier not only met the customer’s specifications but also significantly reduced costs. The strategic material selection, coupled with an optimized design approach, showcases Avantier’s prowess in delivering cutting-edge solutions for complex optical challenges in the medical device industry.
Appendix Figures for Reference